Want to Close the Manufacturing Skills Gap? Think Digital Certificates.
Posted by Penn Foster on January 16, 2019
Make no mistake, the skills gap is real. Ask anyone trying to fill jobs in the manufacturing industry. The pace of technological change means that many people misunderstand the skills that are needed, and some who have them don't see manufacturing as a viable option.
The debate over how to close the skills gap has yielded suggestions ranging from new legislation to hip, millennial-focused PR efforts. Perhaps all of these are needed to create a robust skills force for the future.
In the meantime, manufacturing industry employers need to find a way to get qualified workers onto the production floor and into the design labs as quickly as possible. Digital certificates are that way.
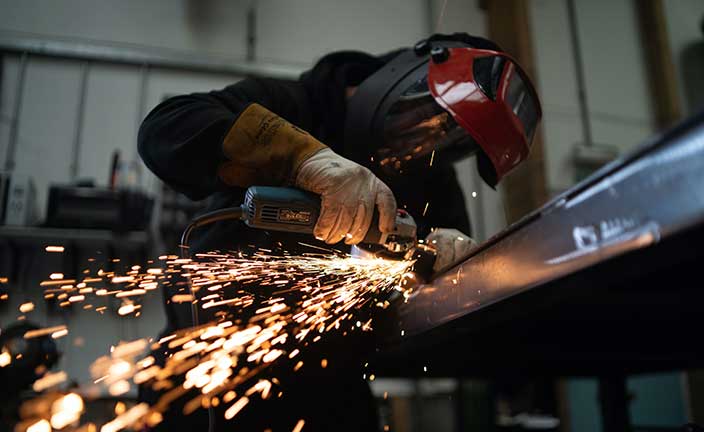
The state of the skills gap in manufacturing
The skills gap is widening, according to a study by Deloitte and The Manufacturing Institute. When the study was conducted in 2015, 84% of executives agreed that there was a talent shortage in U.S. manufacturing. To get a sense of the true scope of the problem, consider that for every six skilled production positions ten go unfilled due to talent shortage.
Causes of the skills gap are hotly debated. Some blame the retirement of baby boomers, unrealistic employer expectations, or the poor public image of the industry for the lack of workers.
Whatever the cause, Deloitte estimated that 3.5 million manufacturing jobs would need filling between 2015 and 2025. Of those, two million were expected to go unfilled due to the skills gap.
What skills are lacking
With all this talk of a skills gap, it's surprisingly hard to identify what specific skills are lacking. One analysis of hundreds of thousands of job postings found that employers in manufacturing are looking for workers with the the following skills:
- Welding
- Machining
- Fabrication
- Computer-automated technologies
- Good manufacturing processes
- Quality control
- Industrial design
- Management and efficiency
These are all technical or high-level skills that relate specifically to the manufacturing industry. However, manufacturing also faces the same challenge impacting other industries - the struggle to find employees with appropriate soft skills to do the job.
According to LinkedIn, the four most in-demand soft skills across industries are leadership, communication, collaboration, and time management. Computer and technology skills and project management skills also show up on many lists.
Finding employees with the correct blend of manufacturing-specific skills and general soft skills is a challenge that will get more difficult as the job market tightens.
How can digital certificates help
Employers and educators have tried a range of options to narrow the skills gap, from helping kids discover a love for STEM to partnering with local colleges. These programs have seen some success, but they tend to suffer from two major defects.
First, they take too long. Getting students excited about manufacturing is valuable, but you need qualified employees today, not in eight or ten years when those students graduate. Second, they're localized. So your manufacturing plant in Scranton, Pennsylvania has a solution, but what about the Boise, Idaho branch?
While legislation and additional funding could help make more learning opportunities available to more students, those students take years to complete their courses. That's on top of the time it takes for legislation to be enacted.
Digital certificates are a superior solution because they work in a matter of months rather than years and they are location independent.
They are not traditional two-year or four-year degrees, and that's a big advantage. Most take a matter of months, not years, to complete.
While a two-year or four-year degree provides students with a well-rounded education, a digital certificate is like a spot weld to fill a hole in employee knowledge. It focuses just on the gap to help employees learn the specific skills they need for their specific job.
Most importantly, employees can continue to work full-time while completing their digital certificates after hours. They're self-paced, online, and mobile friendly, so employees can expand their skills on the bus on the way to work, during their lunch break, or after the kids go to bed at night.
In addition to course materials, employees get access to support staff, fellow students, and a network of industry-trained instructors and advisers.
Which digital certificates are right for my workforce
Whether you need to train new employees from the ground up, or want to provide current employees with a refresher on key concepts, there's a digital certificate for that.
These certificates are just a sampling of what's available to help your employees develop manufacturing-specific skills:
- Machinist Training - Teaches employees to understand machines, their operation, and the underlying concepts of manufacturing.
- Industrial Safety - Your employees will learn how to work safely across electrical, chemical and other environments in compliance with OSHA regulations and best practices.
- Facilities Maintenance Mechanic Training - Prepare your employees for success in maintenance positions.
- Welder Training and Welder Helper Training - Helps employees develop the skills to weld safely and effectively.
You can also support soft skills learning with digital certificates in:
- Basic Business Literacy - Teaches your employees to write and communicate professionally.
- Basic Business Math - Reinforces basic math skills and applies them to a business environment to support problem solving and solution building.
- Basic Skills Training - This wide-ranging course packages math, writing, blueprint reading and safety programs together, ensuring that your employees have all the basic skills they need to succeed.
How do I make them part of my training plan?
Penn Foster has more than 3,000 courses that cover more than 35 occupational pathways.
To make one, or a selection, of these digital certificate programs part of your training plan, contact Penn Foster.
We'll help you identify your greatest skills gaps using our assessment solution. Then we'll work with you to tailor a training or apprenticeship program to the unique needs of your workforce.