Manufacturing Needs People
Posted by Emma Rose Gallimore on November 27, 2019
For decades, the word on the factory floor has been that robots would replace manufacturing workers any day now. That day, if it ever comes, is still far in the future. In the meantime, manufacturing still needs people to do what robots can’t do, or can’t do well.
For leaders in the manufacturing industry, the knowledge that they need employees is offset by the awareness that finding those people isn’t easy. A survey by SCORE found that 89% of manufacturers struggle to fill open positions, exacerbated by an ever-present skills gap that some expect to cost the U.S. up to $2.5 trillion over the next 10 years across all industries.
However, unlike in many other industries, manufacturing leaders have a fairly clear understanding of why their skills gap exists. Three reasons: one, retiring baby boomers; two, misconceptions; three, technology. Industry leaders can’t do much to address the first reason, but the other two are well within their power to change.
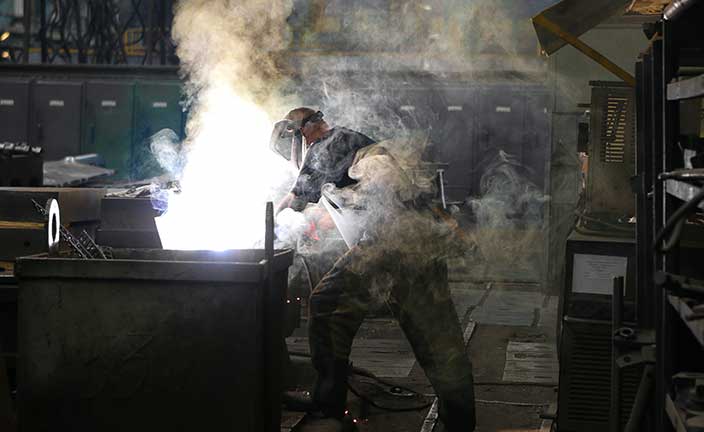
What are the misconceptions about manufacturing?
There are two big misconceptions challenging the manufacturing industry. Strangely, these two ideas contradict each other. The first is that manufacturing is a dirty, dangerous job that no one would willingly take on.
When some people think of manufacturing, visions of the industrial revolution loom large. They picture loud, coal-dusted production floors and dangerous machines. The truth is, manufacturing is safer and cleaner than ever, thanks in large part to new technologies that enable faster production with less risk. Manufacturing companies value their production teams and their reputations, so they enact health and safety rules to protect everyone involved.
While some workers carry a vision of manufacturing plants past, others are looking to the future with an equally pessimistic eye. They believe that technology will remove human workers from the factory floor, replacing them with robots. There’s no point in pursuing a manufacturing career, their thinking goes, you’ll only lose it when robots make you obsolete.
The first misconception is easily dispelled by walking a modern production floor. Since many young people, never do so, it’s up to manufacturers to publicize the safety and cleanliness of their updated facilities so workers can envision themselves building a career there.
The belief that technology will do away with human workers is harder to dispel. Many manufacturing companies really are turning to robots to close skills gaps and perform menial tasks. However, that doesn’t mean manufacturing can survive without human workers. Humans are as vital to the manufacturing process as ever, and will continue to be so for decades to come.
Will robots replace workers?
The impact of automation on the future of work is often smaller than alarmists claim. When you consider that many manufacturers can’t fill the jobs they have now, automating parts of their operation is probably a good thing.
According to an Oxford Economics report by 2030, robots will replace about 20 million manufacturing jobs worldwide. It sounds like a huge number, but it’s only 8.5% of the global manufacturing workforce. And the statistic is deceptive.
Instead of completely overtaking human jobs, robots remove the need for repetitive low-skill labor. As a result, the workforce shifts. MIT Center for Digital Business Director Erik Brynjolfsson calls this process creative destruction. As old jobs are destroyed or reconfigured by automation, new jobs are created. As a result, the number of people who actually lose their jobs to automation will probably be far less than 20 million globally over the next 10 years.
Apply this concept to manufacturing and it’s clear that humans will always be needed to do the jobs that technology can’t. Jobs will become more specialized, with robots doing what they do best—rote manual tasks, leaving humans free to do what they do best—manage people, interact with each other, problem solve and improve processes.
Who is a good fit for manufacturing?
So it’s clear that manufacturing needs people, but which people? Simply convincing more people that a job in manufacturing is a good idea won’t address the persistent talent shortage plaguing the industry. At least, on its own.
If manufacturing companies want to close the skills gap now and in the future, they’ll need to supplement their new technology with quality skills training.
In July 2019, President and CEO of the National Association of Manufacturers, Jay Timmons and Manufacturing Institution Executive Director Carolyn Lee signed a pledge to provide training opportunities to more than 1.18 million manufacturing workers over the next five years.
"With a record number of job openings right now—and many more expected over the next decade—the future of the manufacturing industry will be tied to the future of its workforce," Lee said in a press release.
Manufacturing business leaders can do their part to close the gap by providing workers with skills and technology training. Workers need not be experienced, but they do need to be enthusiastic and willing to learn. Apprenticeships, online learning and skills playlists can prepare new and experienced workers to meet the changing demands of the manufacturing industry.
As an added bonus, training and apprenticeship programs help dispel the myth that manufacturing is a dead-end job. If you’re investing in your workers through training and development you show them that they have a future in manufacturing and you want them to be ready for it. You attract curious, enthusiastic new hires and help experienced workers stay in the job longer by keeping up with industry changes.
If manufacturing needs people, and for the foreseeable future it does, then those people need quality training and development solutions. Rely on Penn Foster to help you choose the right training and development programs for the people who keep your manufacturing plant running.